„Learning to See – Materialfluss, Informationsfluss und Zeit in einem Produktionsprozess auf einen Blick.“
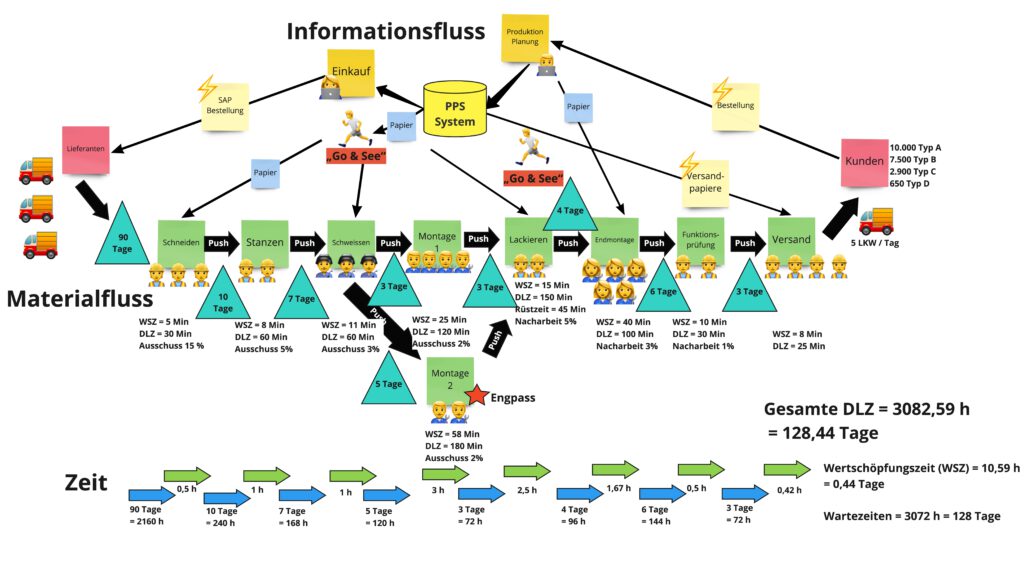
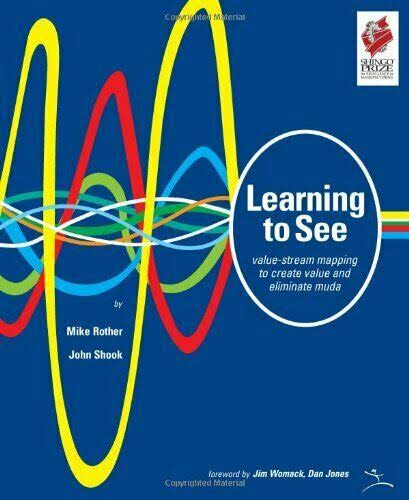
Die bei Toyota entstandene und von Mike Rother und John Shook in ihrem Buch „Learning to See“ 1998 beschriebene Methode Value Stream Mapping (Wertstromanalyse) ist hervorragend geeignet, um den gesamten Produktionsprozesss für ein Produkt oder eine Produktfamilie aufzunehmen. Dazu den Informationsfluss sowie die Zeitdauer für den Gesamtprozess transparent darzustellen.
In meiner Praxis hat sich folgendes Vorgehen in 4 Etappen bewährt:
1. Vorbereitung
1.1 Auswahl einer Produktfamilie / eines repräsentativen Produktes.
1.2 Bildung eines crossfunktionalen Team von Führungskräften und operativen Know-how Trägern aus Produktion, Produktionsplanung, Qualität, Einkauf, Technik, Instandhaltung, IT, Logistik, …
1.3 Kurze Einführung des Teams in die Methode, um einen gemeinsamen Kenntnisstand für das weitere Vorgehen zu haben.
=> Dauer (1-2 Tage)
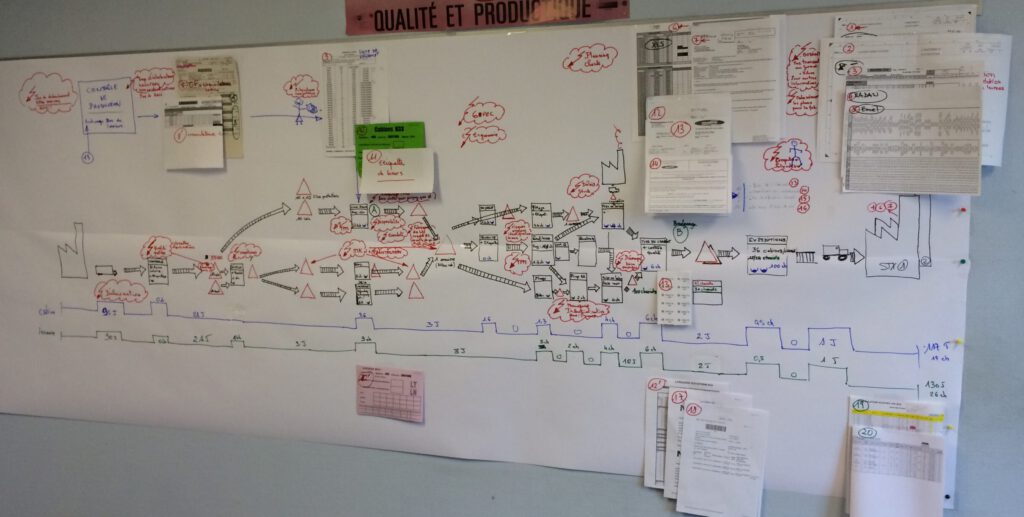
2. Aufnahme des IST-Wertstrom
2.1 Gemeinsamer „Walk through“ durch den Herstellungsprozesses in der Fabrik „flussaufwärts“, zu Fuss vom Versand bis zum Wareneingang, um den aktuellen Prozess als Team mit allen Sinnen zu erleben.
2.2 Darstellung des IST-Wertstrom an einer Wand mit Hilfe der „Brown Paper Methode“ oder digital per Miro Board:
– Aufnahme aller für die Herstellung eines Produktes notwendigen Prozess Schritte
– Anzahl der beteiligten Mitarbeiter im jeweiligen Prozess
– Aktuelle Daten Wertschöpfungszeit (WSZ), Durchlaufzeit (DLZ), Nacharbeitsquote, Ausschussquote, Rüstzeit, Kapazität, etc.
– Darstellung des Materialflusses im Prozess (Push-Prinzip vs. Pull-Prinzip)
– Aufnahme der Bestände im Prozess (geplant, ungeplant, Reichweite)
– Identifizierung der Bottlenecks für den Gesamtprozess
– Aufnahme des Informationsflusses im Prozess (Verbal, Papier, Visuelles Management, Digital)
– Darstellung der Prozesssteuerung („Go & See“, Papier, Kanban, FIFO-Systeme, Digital)
– Ermittlung der Durchlaufzeit (DLZ), Wertschöpfungszeit (WSZ), Wartezeiten im Gesamtprozess
=> Dauer: 2-3 Tage
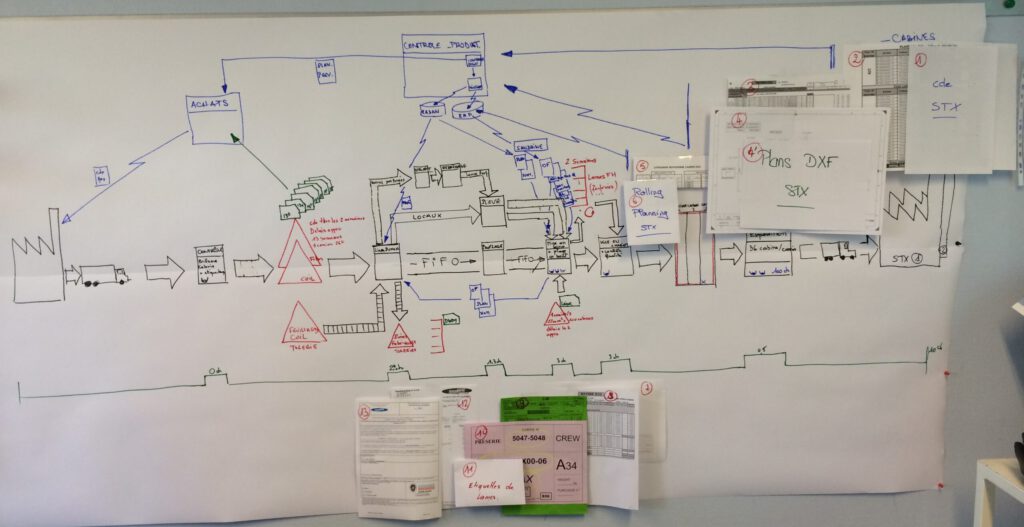
3. Entwicklung SOLL-Wertstrom
3.1 Entwicklung eines idealen SOLL-Wertstrom nach dem „Greenfield-Ansatz“ als Vision für die Zukunft.
– Konsequente Umsetzung von LEAN Prinzipien und Elementen des Toyota Produktionssystem beim Prozessdesign
– Neue Technologien, digitale Lösungen, Modernisierung von Anlagen
– Übersichtliche Darstellung aller Maßnahmen zur Umsetzung des SOLL-Wertstrom
– Priorisierung der Maßnahmen nach Machbarkeit (Kosten, Investitionen, Know-how) und realistischer Umsetzungszeit (kurz, mittel, langfristig)
3.2 Entwicklung eines den Rahmenbedingungen entsprechenden realistischen SOLL-Wertstrom mit einem konkreten Umsetzungsplan für die nächsten 3-6 Monate.
=> Dauer: 2-3 Tage
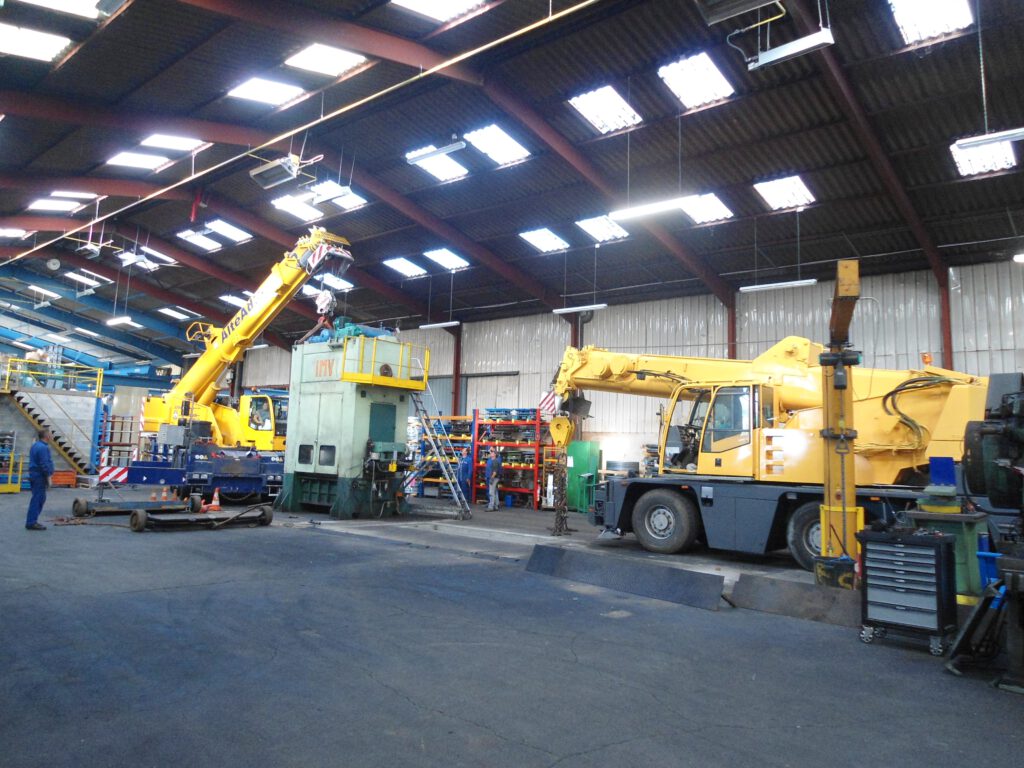
4. Umsetzung des neuen SOLL-Wertstrom
4.1 Agiles Projektmanagement mit regelmäßigen Reviews und Retrospektiven.
4.2 Coaching und Support des Umsetzungsteams vor Ort.
4.3 Gemeinsamer Projektabschluss und „Lessons learned“.
=> Dauer: 3-6 Monate
Value Stream Mapping außerhalb der Produktion
Die Value Stream Mapping Methode ist auch für die übersichtliche Darstellung von Geschäftsprozessen und Serviceprozessen hervorragend geeignet!